Revolutionising cement with biotechnology – Biomason
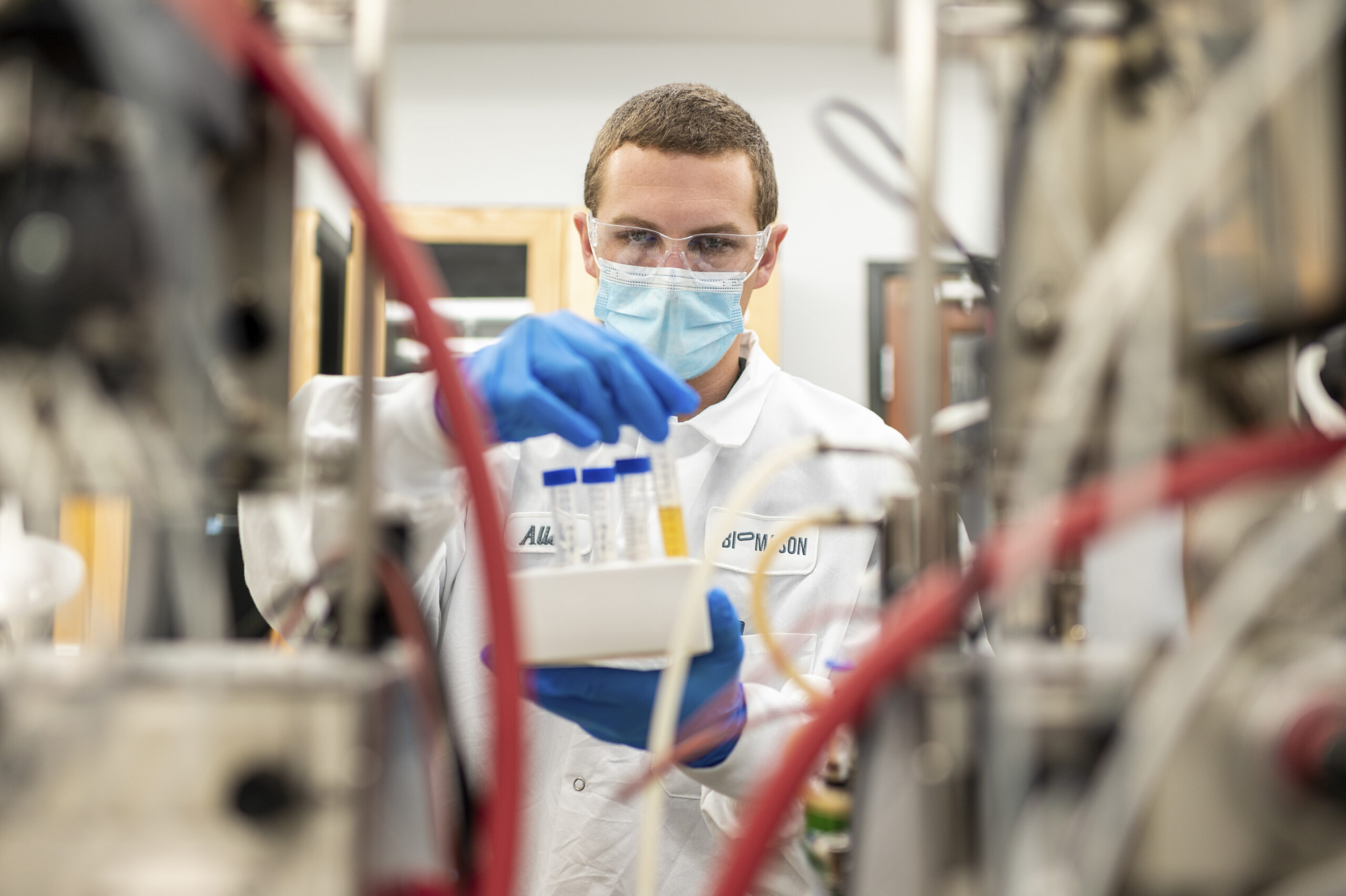
Take a deep dive into how the low-carbon cement recipe from Biomason, one of the core members of our Alliance.
After water, concrete is the most used material on earth. Concrete’s main ingredient, cement, has a significant environmental footprint, accounting for 8% of global CO2 emissions. This type of cement is commonly known as ordinary Portland cement. As demand for cement and concrete continues to grow, it’s more imperative than ever to invest in technology that eliminates construction’s climate impact and to rapidly decarbonise the production of cement.
Biomason was founded in 2012 by Ginger Krieg Dosier and Michael Dosier as a solution to the carbon-intensity of the cement industry.
Biocement – using microorganisms to grow more sustainable cement
The core technologies of Biomason revolve around the creation of Biocement, replacing ordinary Portland cement and working to reduce environmental impacts from the construction industry. One of the main successes of Biomanson’s alternative solution to traditional cement is to use microorganisms to grow durable cement.
Bacterial spores in Biocement material are activated and then precipitate carbon and calcium to produce a biologically forged calcium carbonate — the same material as eggshells, coral skeletons, seashells, and limestone. Biomason’s Biocement technology uses carbon as a building block without the need for kilns to burn limestone. For reference, Portland cement uses limestone as its main ingredient in making clinkers – and the planet cannot afford to continue business as usual.
Step by step: from a bacteria to low-carbon cement
Rather than burning limestone and releasing CO2 like traditional cement, Biocement forms through multiple patented, biological processes, reducing cradle-to-gate carbon emissions by more than 90%. Biomason’s bacteria are introduced in a mix of gravel, sand, and nutrients to convert calcium and carbonate into Biocement. Then, biocement material forms around the aggregate particles, encrusting the gravel and sand in a calcium carbonate matrix, forming concrete.
The bacteria help create a low-carbon alternative to traditional Portland cement. The emissions associated with the process are largely due to supply chain resources, shipping, quarry activities, and electricity, with the potential to realise additional reductions.
We are honored to be a part of the ALCCC to further collaborate with like-minded companies focused on eliminating the carbon footprint within the concrete market. Through this membership we aim to integrate with regulatory, standardization, and certification bodies for developing standards and best practices enabling the urgent transition to planet friendly construction materials.Ginger Kreig Dosier, CEO, Biomason
Get to know us better – Biomason and the Alliance for Low-Carbon Cement and Concrete
Biomason® is a team of biologists, architects, and engineers developing a revolutionary Ordinary Portland Cement (OPC) replacement using advanced biotechnology to reinvent traditional cement and offer a planet-friendly alternative. Over the last 10 years, Biomason has developed their first generation Biocement® – the resulting material functions similarly to OPC but does not require the use of fossil fuel-fired kilns or calcination of limestone, the two major sources of carbon emissions in the OPC manufacturing process. Learn more about Biomason here.
Our Alliance was created to steer the sector towards viable decarbonisation pathways. Our members represent mature materials designers, producers, and start-ups working in biotechnology, capturing carbon, and sustainable construction. We are all rooted in the circular economy and sustainable construction, and we all share the desire to change our industry – and prevent catastrophic climate change.